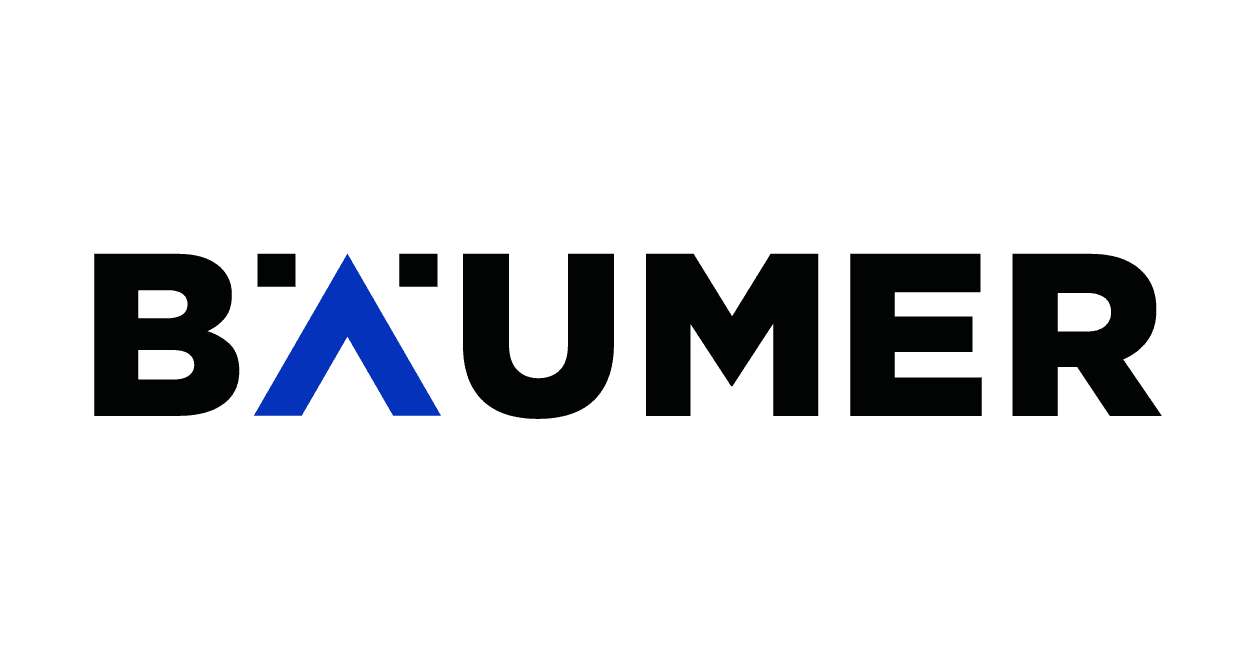
Support for warehousing
at Albrecht Bäumer
Find out how Albrecht Bäumer managed to save time, reduce error potential and complexity and how they avoid inventory discrepancies.
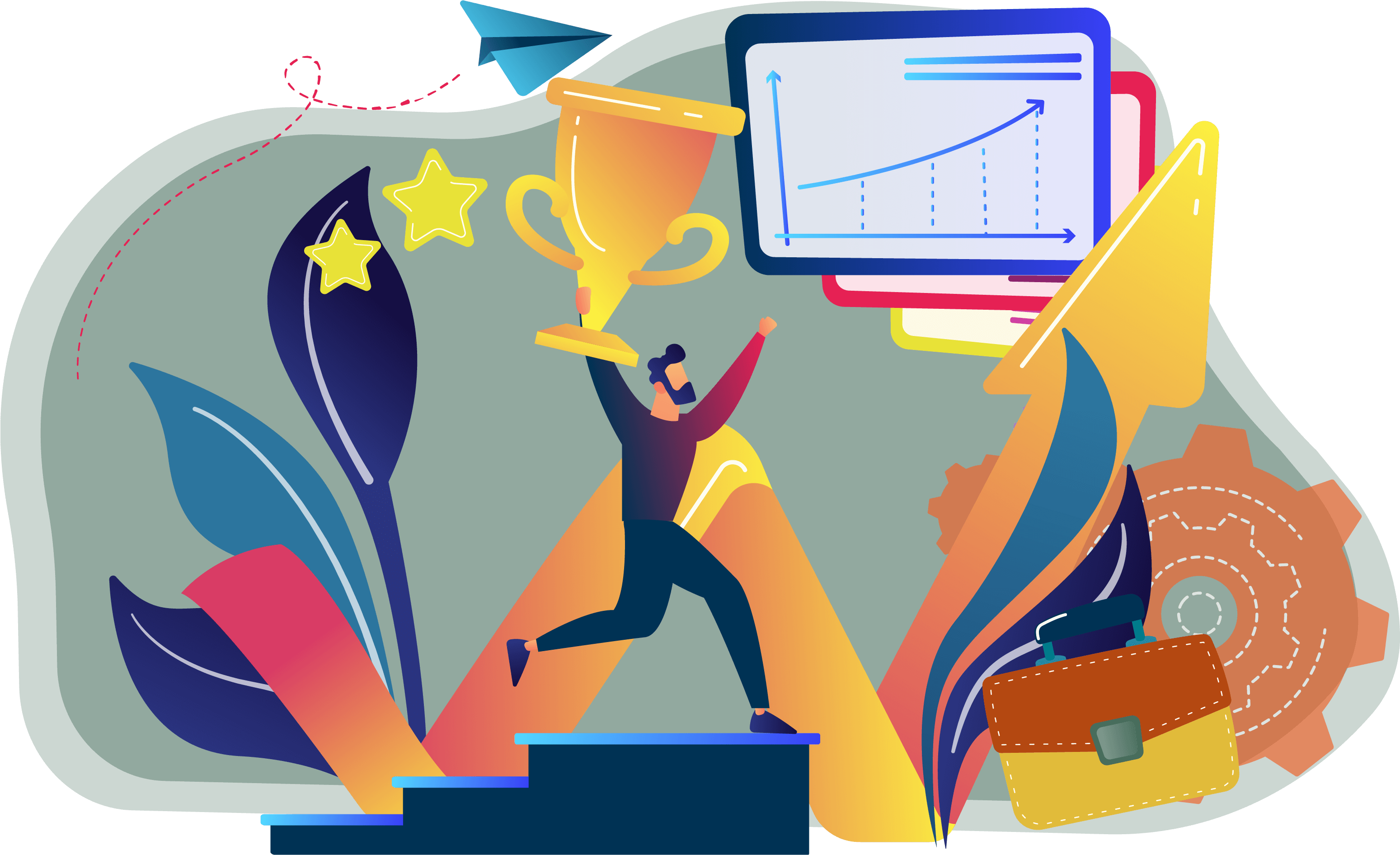
Everything At A glance
YAVEON ProE-SCM: Scanning
Customer
Albrecht Bäumer GmbH & Co. KG | www.baeumer.com
Focus
Mechanical and Plant Engineering
Company Size
approx. 350 Employees
Operating Model
On-Premises
Country
Germany
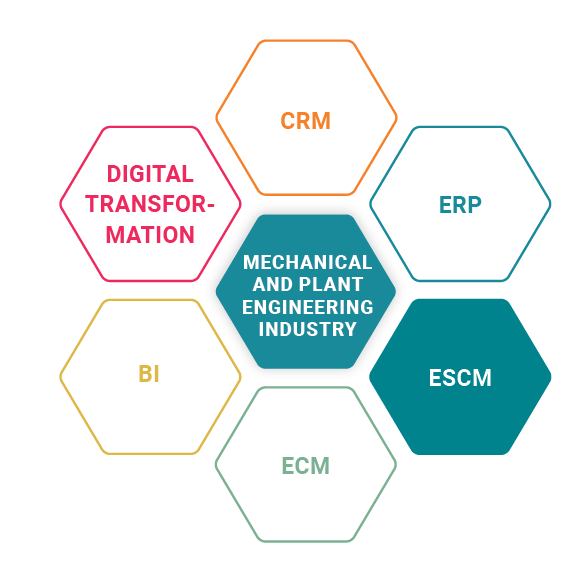
Want to read the reference report in one document?
Sure - simply download the PDF version of the report
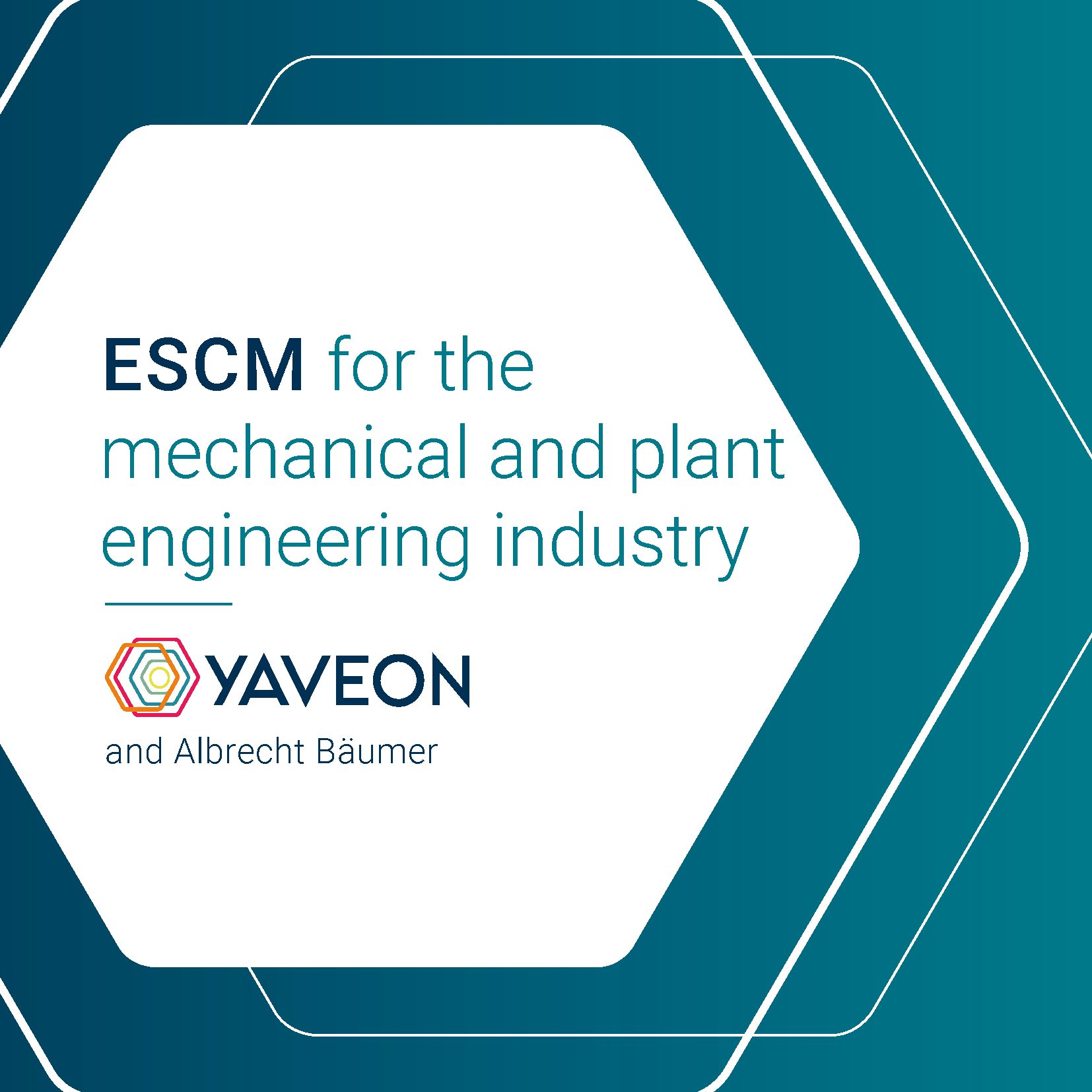
Which benefits does the YAVEON solution offer?
Visible results
Challenge
- Tangible support for
warehousing, which also
allows the secure processing
of outgoing spare parts - Scanning solution
- Simplifying the zero-error
principle
Solution
YAVEON ProE-SCM Scanning module
Use
- Time saving
- Reduced error potential
- Reduced complexity
- No inventory discrepancies
- Punctuality
Tradition and international growth
The Albrecht Bäumer GmbH & Co. KG
Just imagine... The doorbell rings. You jump up, full of anticipation, and take the box from the postal worker. You quickly get the scissors, cut the tape and open the box. The long-awaited item is in your hands, and it is exactly what you wanted.
But think about how you would have felt, if the wrong item had been delivered. You would be disappointed and perhaps irritated - not an ideal result. Packing mistakes happen, though thankfully fairly rarely. In most cases, when you open your package, you receive the product that you ordered. And this is due to the goal of companies to satisfy their customers.
The goal of keeping customers happy doesn’t just apply to private shopping activities, but also to the business world. That’s why Albrecht Bäumer, a medium-sized machine and plant manufacturer, works on the principle of offering customers maximum convenience and even goes one step further: The company sets itself the goal of a zero-defect strategy. How does this work?
Securing the future of our customers through customer-specific engineering and intelligent services.
Albrecht Bäumer is a manufacturer of foam cutting machines and provides solutions ranging from a small stand-alone machine to entire foam plants for a highly divergent clientele. With customer-specific engineering and intelligent services, the team wants to pave the way into a secure future for its customers. Albrecht Bäumer is one thing in particular: A leader in quality. The foam is cut precisely, resulting in extremely durable products. A further feature is that their customer service extends far beyond the order. With their own after-sales-service, the technical sales team is always available to answer customer questions. A separate department deals with spare parts. This naturally raises the question: What is the best way to organize the spare parts distribution?
YAVEON and MODUS Consult - a partnership that advances customers
Albrecht Bäumer realized the implementation of the new ERP system with the business IT partner MODUS Consult. The machine manufacturer was specifically looking for a solution for the outgoing spare parts department. A criterion was that the system should work with devices for mobile data acquisition. In the future, the handwritten lists should be replaced by hand-held scanners. “MODUS Consult told us about the partner solution YAVEON ProE-SCM as well as the corresponding scanning module and established the contact with YAVEON”, says Peter Paetzold, Lean Management Consultant at Albrecht Bäumer. The YAVEON consultants presented the solution and impressed the Albrecht Bäumer team - the project could start.
What can YAVEON ProE-SCM Scanning do?
- Fully integrated with Microsoft Dynamics NAV/365 Business Central
- Logistics can be fully digitized via scanner devices
- Automates the cross-system data exchange
- Can be extended by further modules if required
What does Albrecht Bäumer mainly use?
- Warehouse support features
- Picking and packing - mapped in the same system
- Packaging and shipping proposal
- Delivery proposal and delivery orders with scanner solution: Checks and verifies that all data match and are correct
A partnership of equals leads to success
The partners YAVEON and MODUS Consult carried out the project with regular consultations; the implementation of the EDI Solution was completed by YAVEON independently. Peter Paetzold always had a good relationship with his contacts and regards the project in a positive light. Of course, as in almost every project, Albrecht Bäumer also faced challenges. For example, the software structure had to be adapted to differentiate between packing and wrapping, as well as the 130,000 identification numbers of the foam specialist. “At first, it was a challenge”, Peter Paetzold said, “but we had a constructive conversation with our YAVEON consultants and found a solution”. And the same was true of the perhaps the biggest hurdle: weighing. Albrecht Bäumer checks every single weight before shipping. In order to be able to display this directly in the software, YAVEON developed an own level to which Albrecht Bäumer’s scale and the EDI module were connected. With a plausibility check, Albrecht Bäumer can compare the weights and prove that everything was packed and picked as ordered. This provides certainty and prevents breakdowns - in line with the zero-error principle. “The process worked very well. We were particularly pleased that parts of our customization were incorporated into the standard software,” Mr. Paetzold recalls. The Lean Management Consultant felt that he was in good hands at all times and could always talk to his contact persons on an equal footing. “Our YAVEON consultant was always there for us. He can also read source code and immediately knows how to deal with it. That’s not always the case.”
"The process worked very well. We were particularly pleased that parts of our customization were incorporated into the standard software."
Mr. Paetzold, Albrecht Bäumer GmbH & Co. KG
YAVEON ProE-SCM
What advantages does the scanning module offer?
The solution Albrecht Bäumer now uses has many advantages. The main ones are:
- Time saving: Employees used to have to walk from A to B with labels but now digital labels arrive digitally exactly where they are needed. Print, stick, done.
- Reduced error potential: Mistakes are less common due to the provision of labels and the processing with the scanner.
- Reduced complexity: As the software is used for picking and packing, both processes are carried out in a closed system.
- No inventory discrepancies: Inventory differences are avoided through the detailed weighing function.
- Punctuality: Thanks to the proposal function, even time-critical orders can be handled reliably.
Achieving zero-error
The declared goal and also the aspiration of the Albrecht Bäumer team is maximum customer satisfaction. To achieve this, the company focuses on quality, sustainability and customer service that goes beyond the actual order. With the scanning module of the YAVEON ProE-SCM solution, Albrecht Bäumer has opted for software that reliably digitizes processes and enables full control during dispatch. No stone is left unturned in the long-term effort to fully meet their aspiration of zero-error.